In the ever-changing world of construction, the combination of Prefabrication and Building Information Modeling (BIM) is a significant force, transforming how projects achieve efficiency, safety, and sustainability. For MEP contractors, it's crucial to comprehend the methods for aligning BIM and Fab Shop teams to fully leverage this powerful synergy. Let's explore how BIM can smoothly integrate with prefabrication, fostering a seamless collaboration that leads to improved project results.
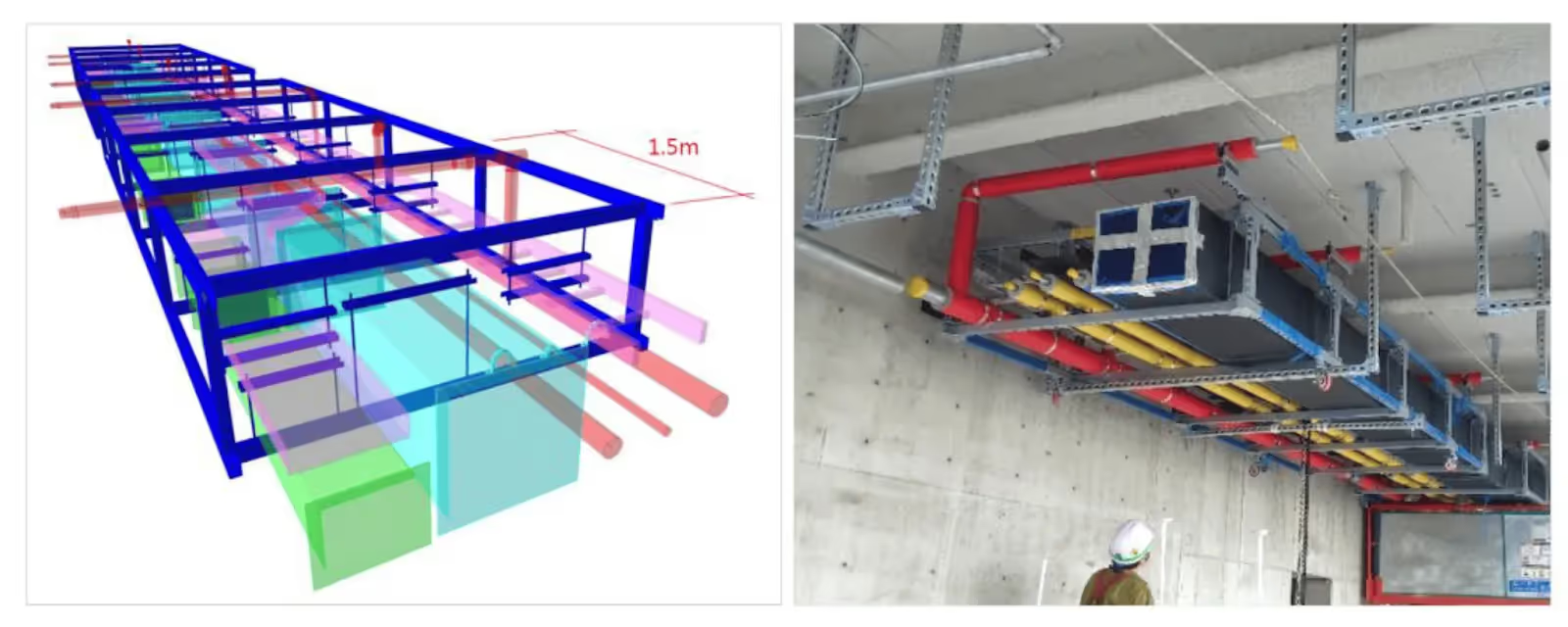
Reduced Waste and Sustainable Sourcing:
The practice of prefabrication consists of sustainable construction principles through careful planning and sourcing from local, sustainable suppliers. This approach lessens the environmental impact associated with transportation and packaging, making it an ideal choice for clients in search of environmentally friendly solutions.
Faster Construction for Energy Efficiency:
Prefabrication's off-site construction accelerates project timelines while aligning with energy efficiency objectives. By minimizing on-site construction time and reducing energy consumption, it presents a sustainable and eco-conscious approach to building.
Greater Flexibility for Optimal Land Use:
The adaptability of prefabrication allows for the easy disassembly and relocation of buildings, promoting optimal land use. This feature mitigates the environmental impact of urban sprawl, making it a crucial element in sustainable urban development.
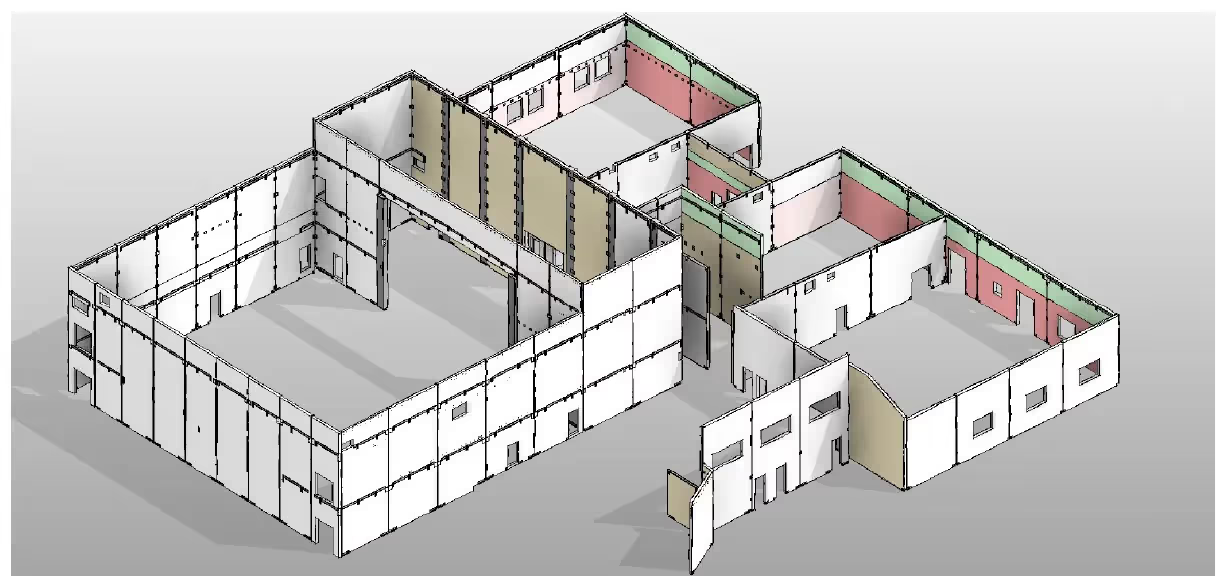
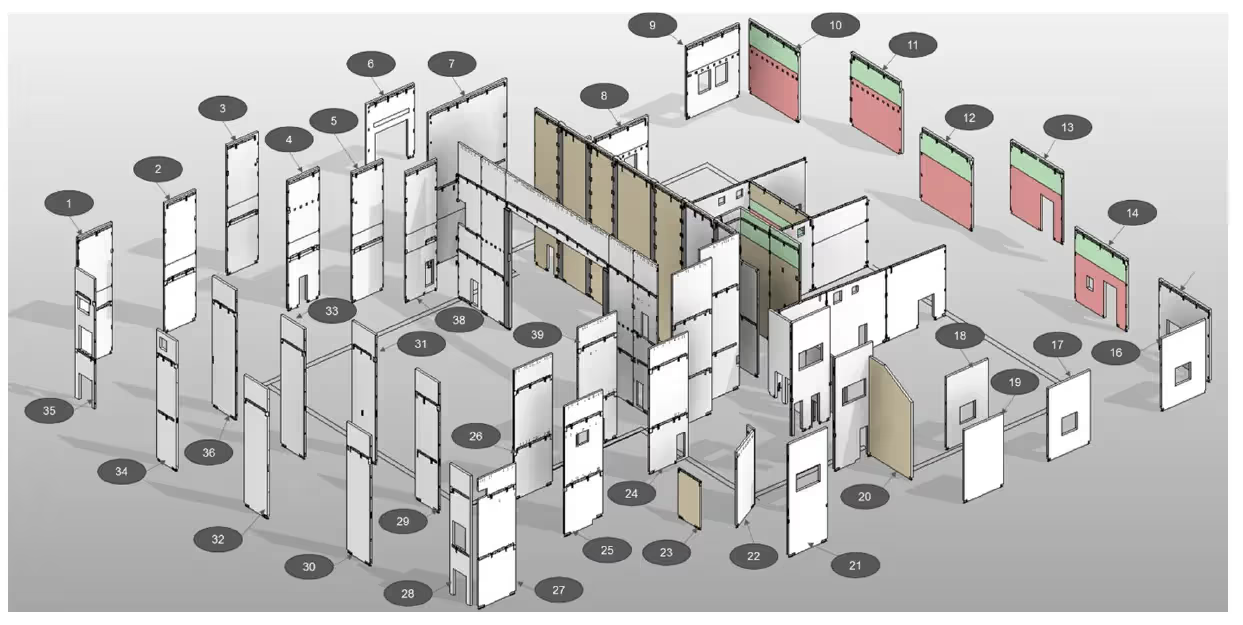
Prefabrication for Time and Cost Savings:
Accelerated Construction Timeline:
The swift delivery and on-site assembly of prefabricated components expedite the construction process, resulting in substantial time and cost savings. Independence from weather conditions further contributes to an expedited timeline.
Reduced Labor Costs and Waste:
Shorter build times lead to reduced labor costs and on-site adjustments, minimizing the demand for skilled workers and contributing to waste reduction. Precision in prefabricated components ensures efficiency and cost-effectiveness.
Savings Across the Board:
Prefabrication provides various opportunities for cost savings, spanning transportation, logistics, materials, and bulk purchases. The factory-based manufacturing process guarantees efficiency, enabling MEP contractors to optimize budget allocation.
Safety Amplified Through Prefabrication:
Reduced On-Site Risks:
Prefabrication, primarily conducted off-site, diminishes on-site worker risks. With fewer workers present, the potential for accidents resulting from overcrowding or inadequate supervision is significantly reduced, fostering a safer work environment.
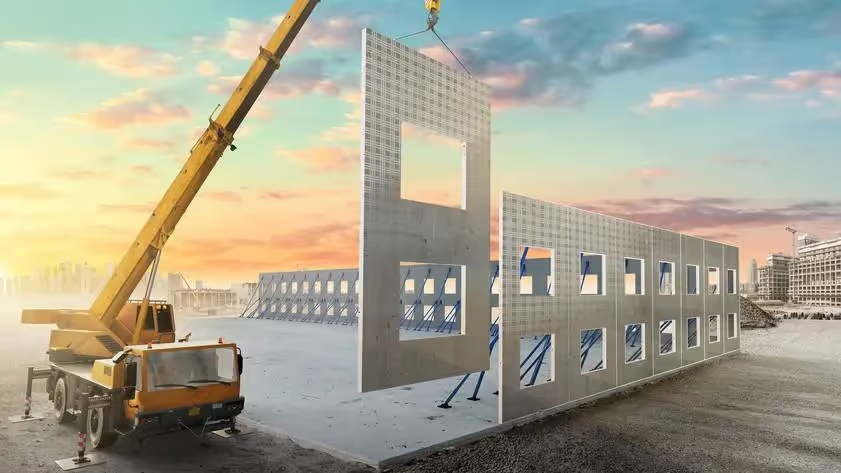
Aligning BIM and Fabrication Shop Teams for Optimal Impact
Building Information Modeling (BIM) plays a crucial role in enhancing the advantages of prefabrication. The integration of BIM with prefabrication methods introduces a new level of efficiency, safety, and sustainability. Here's how your BIM and Fabrication Shop teams can align for maximum impact:
Coordination
BIM's 3D modeling software generates detailed MEP system models, facilitating seamless coordination among various trades to identify and resolve conflicts before reaching the construction site. This ensures precision and efficiency in the prefabrication process.
Fabrication
BIM-generated models aid in creating detailed fabrication drawings and bills of materials, streamlining the prefabrication process. Ready-to-install pre-manufactured components reduce on-site assembly time and costs significantly.
Quality Control
Detailed inspection and testing protocols, created by the BIM department using models, ensure that prefabrication components meet required standards. This rigorous quality control process minimizes defects and rework, ensuring a final product of high quality and safety.
Logistics and Scheduling
BIM-generated schedules and logistics plans optimize the prefabrication manufacturing process, ensuring components are ready on time and in the right place. This streamlined approach reduces construction delays, resulting in time and cost savings.
Maintenance
BIM models contribute to the creation of detailed operation and maintenance manuals, facilitating easy facility management. This ensures that building systems are well-maintained, operate efficiently, and contribute to long-term energy cost savings.
Lean Construction
Leveraging BIM models, teams can identify construction inefficiencies and implement lean construction methodologies like the "Last Planner System" or "Pull Planning." This strategic approach reduces waste and enhances overall construction efficiency.
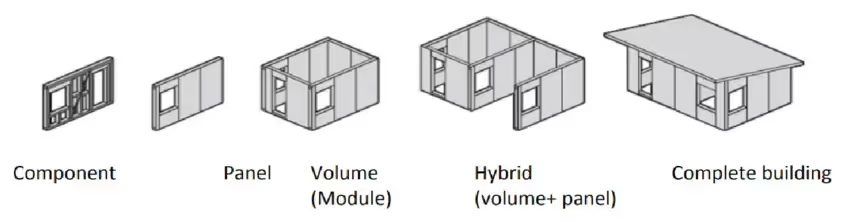
Effective communication and collaboration are essential for successful alignment between the BIM department and the prefabrication shop. Working closely and sharing information ensures a smooth and efficient process, ultimately reducing costs, improving efficiency, and delivering a final product of high quality.
In the era of construction management technology, collaboration has become more accessible. With project documents, progress tracking, and BOM management centralized through BIM, your teams can collaborate seamlessly. This technological synergy promotes improved communication, team connectivity, and enhanced visibility, laying the foundation for unparalleled collaboration between your BIM team and the prefabrication shop.